Moisture Content
moisture meters
moisture meter manufacturer
restoration professionals
restoration project
Quick Fixes for Common Moisture Meter Issues


Although moisture meters serve as a quick, accurate and effective way of keeping structures and various materials up to code, they can also break or fall down on the job. Like all machinery or intricate equipment, they need tender loving care in order to continue providing value. Part of making sure your moisture meter is doing its job effectively has to do with regular maintenance and keeping an eye on its functionality.
Of course, some unforeseeable circumstances can prevent a meter from functioning. And this is why it’s important to note the most common instances where meters fail and the methods in which to fix them quickly.
Malfunctioning Displays
Sometime, your moisture meter has trouble with the way the numbers are portrayed on its screen. The numbers may appear faded to the point where it’s difficult to determine the actual reading. For instance, an 8 may look like a 6 or a 7 may appear to be a 1 with part of the screen being shaded dark.
This problem can be a result of having a low or dying battery. If you’re able to determine that’s not the issue and the problem persists, then it could be that the meter is due for servicing, and could mean that the digital display needs to be replaced.
Solution: If this is your problem, replace your battery and see if the screen appears to be brighter and more functional. In the worst case scenario, you can send your meter to its manufacturer and they should be able to fix the problem and offer and explanation.
Wrong Readings
If you’re measuring a material or building structure and the meter reading seems off, this can be extremely annoying and even dangerous. As you rely on these meters for accuracy, this flaw can be time consuming as you’ll have to find an alternate strategy to measure moisture.
If you’re unsure of your meter’s accuracy, test the same area twice. If the meter gives you two wildly different readings, then there’s an issue.
Solution: If your meter has pins, take a look at them. Is there damage? Are they rusting? If so, then this may not be a “meter problem” as much as it is a “pin problem.” If the pins are in good shape and firmly attached, then the meter should be returned to the manufacturer for repair.
If your meter is pinless, double check the method you’re using when you put the meter to the surface. Is it area being scanned big enough for the meter’s scanning plate? Is the scanning plate in good condition? Are you applying enough or too much pressure when measuring? If none of these are issues, then it’s likely time for you to have your moisture meter serviced.
Prevention
To prevent damage from ruining your moisture meter, there are steps you can take to ensure a high-quality meter.
Checking your battery on a regular basis prevents you from having to waste time figuring out a meter issue is cause by something more severe. Always have an extra set of batteries handy and replace your old ones before you diagnose the problem.
Store your meter in a safe place. While they’re made for heavy duty uses, it’s imperative to keep your meter in its designated box. The padding in an enclosed box helps to keep the small parts within the meter in place as to not cause internal damage and not cost you more than you need to spend.
Find a dry, cool place as very hot or cold or damp temperatures can seep into the meter and eventually tamper with its accuracy.
Analyze your pins on a regular basis. As the pins are made to handle tough surfaces, they are also sensitive. Every time you use your moisture meter, make sure to look at them and look for rust. Also, check that the coating on insulated pins has not worn off, as this can drastically affect your readings.

Subscribe to Our Blog
Post Related

Checking Insulation with Restoration Moisture Meters
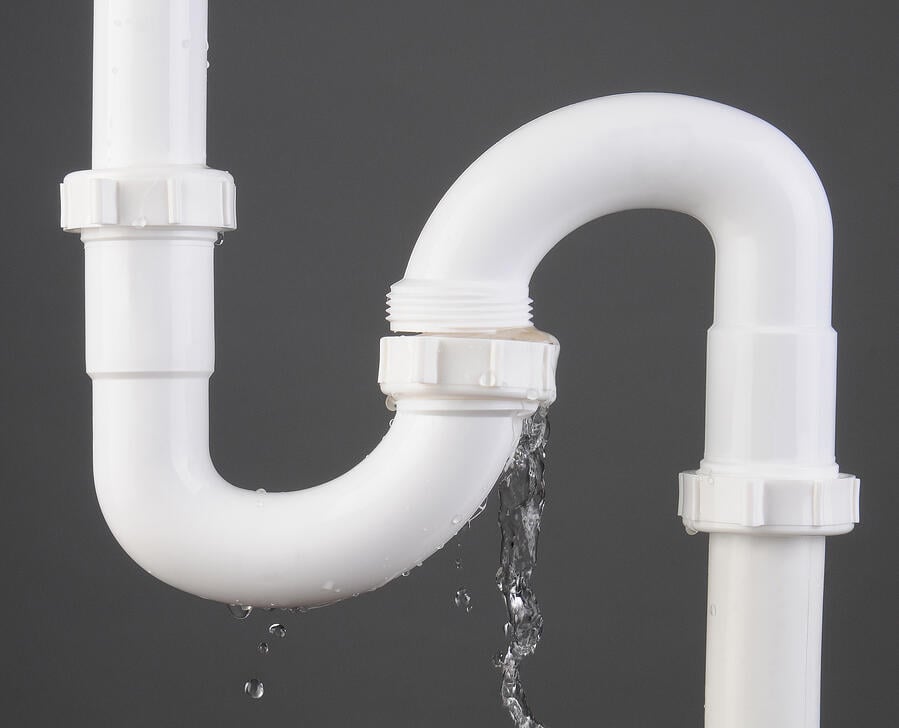