Practical Uses For Moisture Meters For Quality Improvement in Wood Manufacturing RX # 7

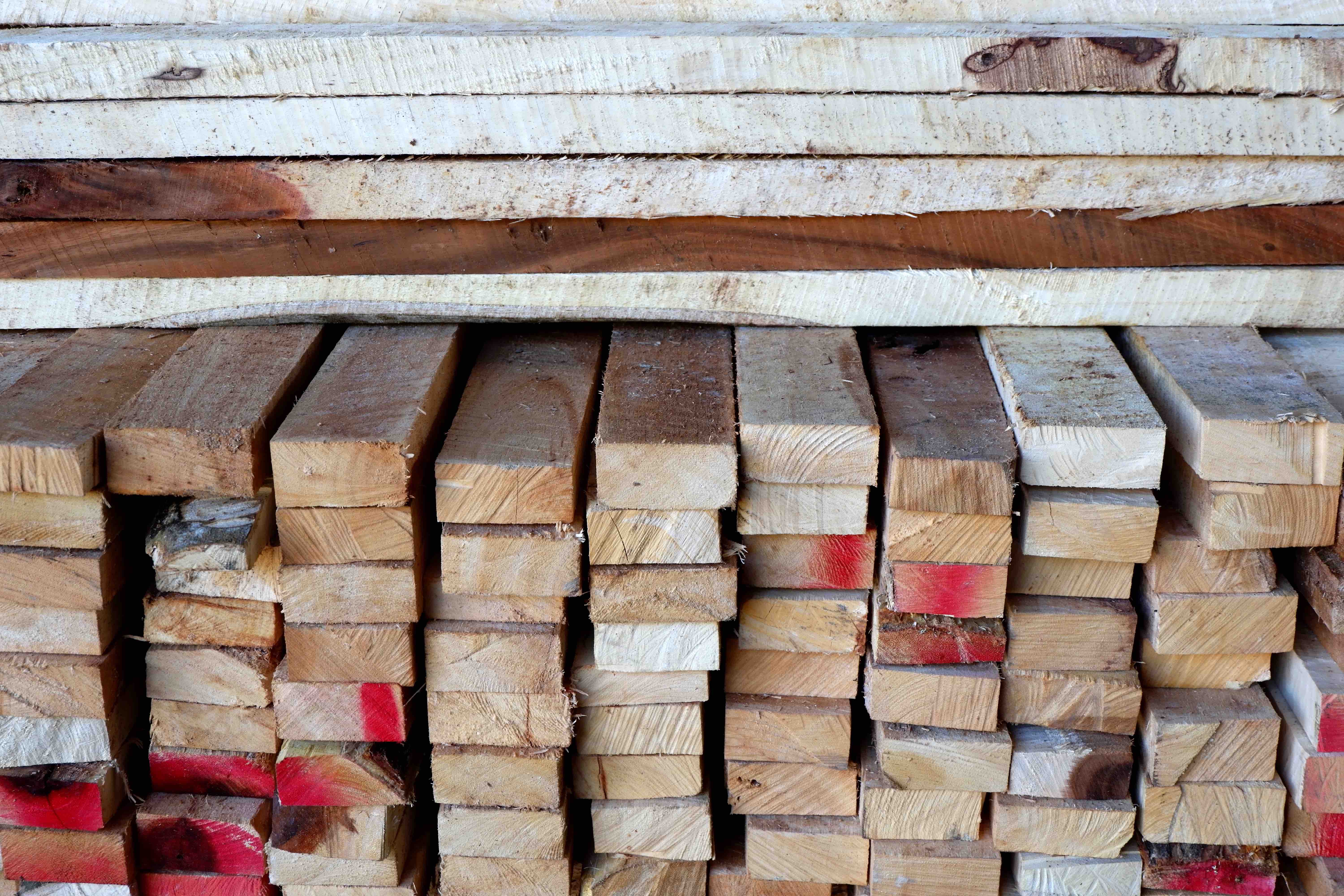
Rx #7: DIAGNOSING CUSTOMER ISSUES
Every so often, but hopefully not too often, a customer has a complaint. Often, moisture content (MC) is the potential issue. So, let’s discuss how to use a moisture meter on many types of finished products to obtain the necessary MC information.
Complaint: Wet lumber
The best defense against shipping wet lumber or wet products is to measure the MC of the lumber or wood product just prior to shipping. This can be done with a pin- or pin-less meter.
Once wood is shipped, the core MC will be very slow to change. So, measuring the core will almost always give us the MC when the lumber left the dry kiln. To get the core MC, use a pin-type meter with insulated needles; only the tips are exposed. Drive the tips into the core (1/2 the thickness). Do not let the nuts holding the needles touch the lumber’s surface. Washers on the pins come with the meter to prevent this; make sure they are still in place.
Complaint: Product got wet in storage.
If lumber or a manufactured wood product gained MC during storage or shipment, then it will, for a short time after storage, have a higher shell MC than the core MC. Use insulated needles and take MC readings approximately every 1/8” in depth from the surface to the core.
Complaint: Over-Dry lumber.
When checking for over-dry lumber (over-dried hardwoods often are MC < 6.0% MC; softwoods, < 10% MC), it might be necessary to use a pin-less meter, as pin meters do not work well under 6.5% MC. The pin-less meter will give e an average MC. Also, check the core MC with a pin meter using insulated needles, as the core is usually the MC when the lumber left the kiln.
Complaint: Checks or cracks opening after finishing.
Dry wood is twice as strong as wet wood, so it will take a lot of MC loss (over 12% MC change) to create enough shrinkage and resulting stress to initiate a new check or crack with dry wood. This applies to lumber, cut-stock and wood parts, and veneer. Therefore, virtually all checks and cracks found in manufactured products are the result of old checks from the lumber or veneer reopening when the wood is exposed to a dry environment, such as normal, wintertime, interior, home humidities. Many times, when we split open the crack or check and look inside, we will see small spots of finish inside the crack indicating the crack was present prior to finishing.
Here is a key: If the wood was very wet when the product was manufactured and then dried out after shipping, will a MC measurement taken on the dry material indicate that the wood was wet? Answer: “No!” The only way we know that the wood was wet when the product was manufactured is to take a moisture reading BEFORE the issue develops. Readings taken after the issue will always be dry readings. Even though the pin-less meter is designed for a specific thickness of wood, a pin-less meter will still come close enough to indicate a potential problem. For precise values, use a pin meter.
Complaint: Lumber or product warped AFTER manufacturing.
The 100% rule is that wood does not change size or shape unless its MC changes. So, when wood warps, we know there is a MC change. Readings after the warp occurs will be low MCs. So, we need to make sure that we have MC readings prior to the occurrence of warp.
When a wood product warps, we know for certain that the wood’s MC did not match the environment’s EMC. Was the wood at the wrong MC or the environment too wet or too dry? Sometimes we can tell by measuring the MC gradient, as described above, using insulated needles. Special note: Completely wrapping lumber or a manufactured product in plastic wrap will prevent any moisture change, as water cannot get in or out of the package, no matter what the temperature or outside conditions.
Complaint: Lumber or wood product shrank or swelled after installation.
Wood does not shrink or swell unless its MC changes. So, if we measure the MC now after changing size AND measure the amount of shrinkage or swelling precisely, we can easily estimate what the MC was before it shrank or swelled. The MC we need is the average for the piece, not shell or core alone; with a pin meter, drive the needles 25% of the thickness; for a pin-less meter, the MC reading is the average.
Complaint: Open Glue joints.
In the majority of cases, the individual pieces of wood were cut with straight edges, but then were allowed to “sit around” for an hour or longer before they were assembled and glued together. During this waiting period, if the piece’s MC was a little higher than the plant’s EMC, the ends of the pieces lost MC and shrank a maybe 0.01”. This small size change means a tiny gap exist at the ends when the panel was assembled; a gap of over 0.006” is the beginning of a weak glue joint. A little more shrinkage after gluing- -in the dry plant, finishing oven, or consumer’s home- -means the shrinkage stress will likely opens the joint. The solution is to make sure the MC of wood is within 2% of the plant’s EMC. Measure these values every 3 hours using accurate equipment. Rapid assembly after preparing the flat surfaces is also important. (A good glue joint is actually 1-1/2 times stronger than the wood itself.; a good glue joint should never fail.)
Complaint: Brittle wood with machining defects.
Softwoods under 10.5% MC and hardwoods much under 6.5% MC behave in a brittle manner. Chip out and splitting are two machining defects often seen. The key to prevention is to avoid over drying the wood. MC checks prior to processing are essential. As sometimes the MC is under 6.5% MC, moisture should be measured with a pin-less meter. (Once over-dried, the wood’s brittleness cannot be easily reduced just by increasing the MC to more normal levels.
Rx is from The Wood Doctor, Gene Wengert, President, The Wood Doctor’s Rx LLC
Subscribe to Our Blog
Post Related
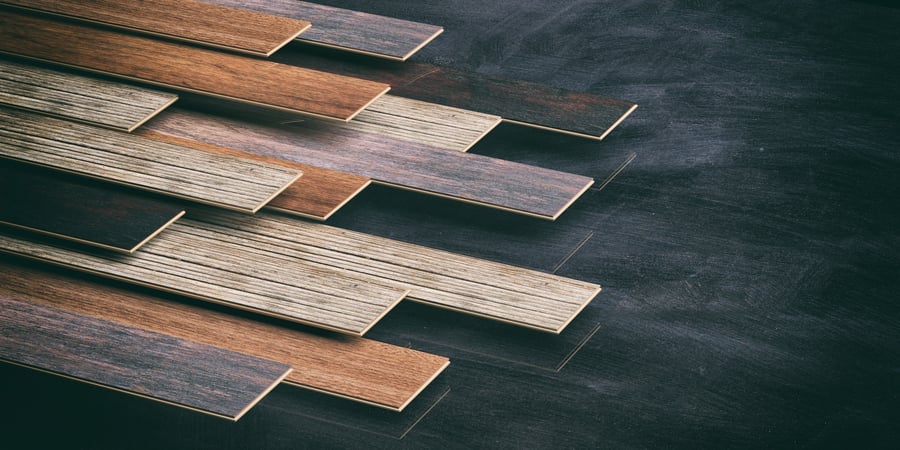
Practical Uses For Moisture Meters For Quality Improvement in Wood Manufacturing RX # 2
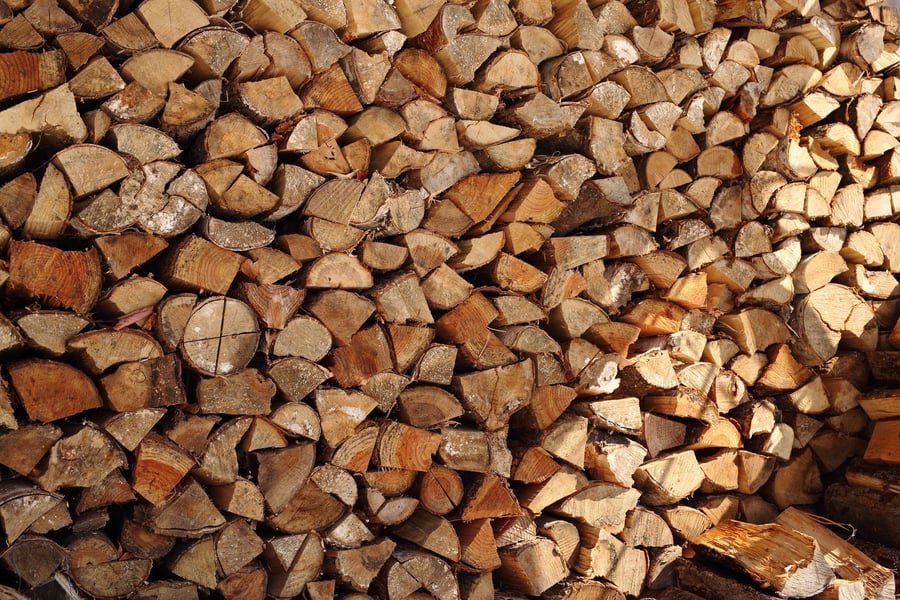