6 Mistakes That Lead to Bad Moisture Testing

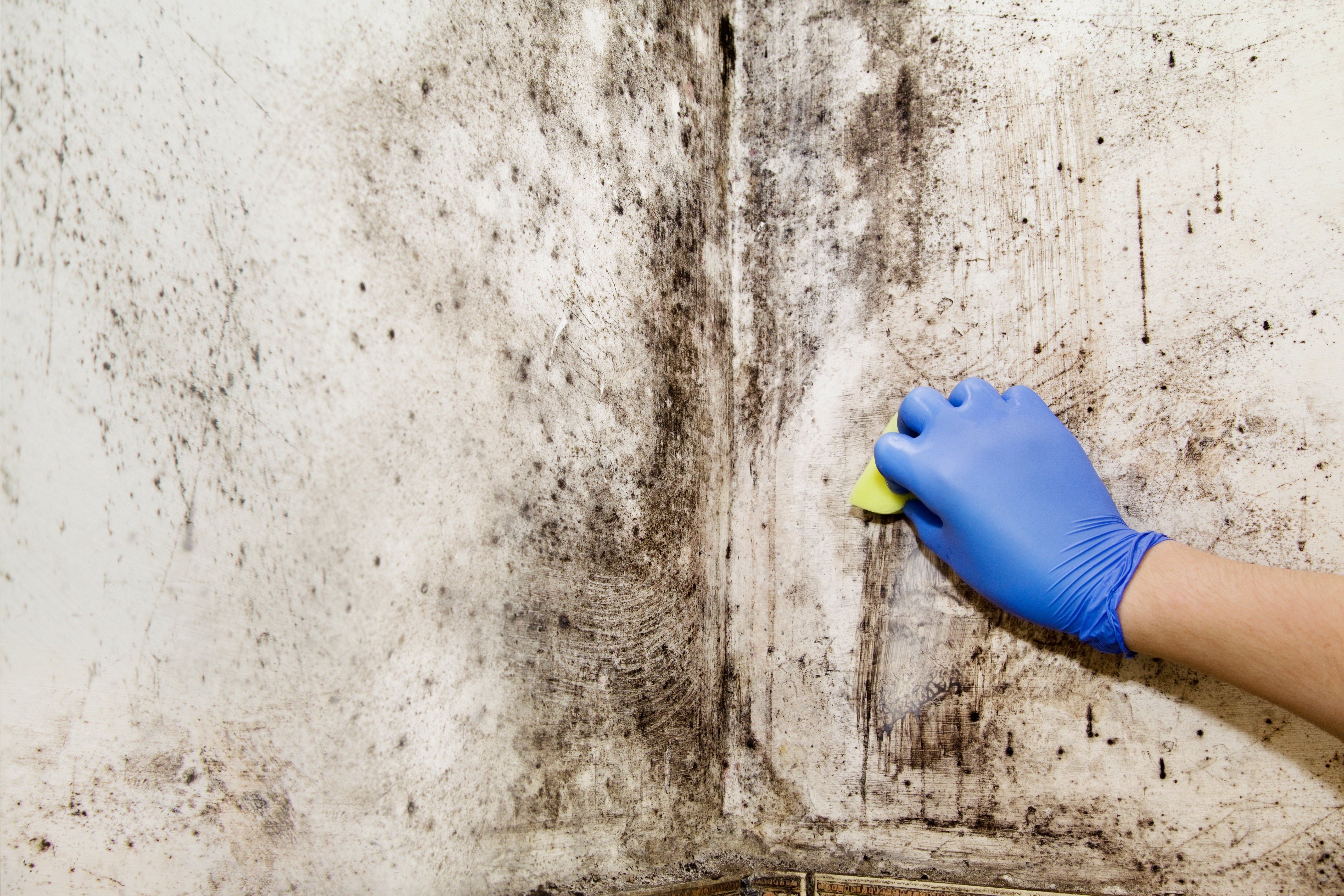
There are many people who need to conduct moisture testing for a variety of reasons. For example, farmers use soil moisture meters to check the available moisture of their soil to manage their irrigation (helping to improve crop yield and quality). Water damage remediation specialists use moisture testing tools frequently o find hidden moisture pockets in buildings. Flooring installers conduct moisture tests to verify that the wood flooring they install won’t buckle, cup, or warp after installation.
These are just a few examples of people who use moisture testing tools for their livelihoods. What these moisture meter users all have in common is the need to get the most accurate moisture measurements they possibly can. If someone uses a moisture meter but doesn’t get accurate assessments of moisture content (%MC), then they could make a mistake based on that bad information which costs time, money, and resources.
Sometimes, people using moisture meters can make a mistake that causes inaccurate moisture measurements. Knowing what these mistakes are is the first step in avoiding them. The following list details some of the most common moisture testing mistakes that users make, and how to avoid them.
Moisture Testing Mistake #1: Forgetting to Replace a Moisture Meter’s Batteries
One of the most common causes of a bad moisture measurement is that the batteries used to power the moisture meter are undercharged. Low battery power keeps the meter from operating at peak efficiency, which can cause erroneous moisture measurements.
Worse — if the meter is put into use with near-empty batteries for too long, it can result in permanent damage to the moisture meter.
How to Avoid This Problem:
The easiest way to avoid this moisture testing mistake is to regularly check the level of charge for the meter’s batteries. If low, the batteries should be promptly replaced with a fresh set. It’s better to spend a couple of dollars on a new 9V battery than it is to need to replace the entire moisture meter.
Moisture Testing Mistake #2: Using the Wrong Type of Moisture Meter for the Job
As mentioned earlier, people across many industries use moisture testing tools on an almost daily basis. However, not every moisture meter is the same. Many moisture meters are specially designed for certain applications and will not provide optimal results if used for a different application.
For example, say someone were to use the KS-D1 soil moisture meter to test the moisture content of hay. Although the KS-D1’s universal probe socket would allow it to use a Delmhorst hay electrode, the meter itself isn’t calibrated for testing hay. The reading the meter would give in such an event would be qualitative, at best, and not nearly accurate enough to use for determining the quality and safety of baled hay.
How to Avoid This Problem:
The simplest fix is to make sure to use the right moisture meter for the job. When choosing a moisture meter, it’s important to consider:
- What materials will be tested most frequently: This is useful for selecting moisture meters with the right moisture reading scales).
- The species of the wood: If testing wood, consider the species or specific gravity of the wood and check to see if the meter has a built-in correction setting for that specific wood.
- How easy the moisture meter is to use: If the meter is too complicated, then it will be difficult for newer users to get the most accurate measurements with it.
- What functions the meter has: Extra features such as built-in species correction, moisture reading recording capability, and electrode compatibility can all help to make a moisture testing tool more versatile and useful—though complex.
Moisture Testing Mistake #3: Using the Wrong Moisture Meter Electrode
Moisture meter electrodes play an enormous role in modifying the meter’s utility. Many moisture meter electrodes are purpose-built for specific applications to help ensure the best possible moisture measurements in those applications.
For example, the 12-E moisture meter electrode has two rolling-pin shaped electrodes that are specifically designed to help the electrode make solid contact with a rolling paper pulp mesh. This makes the 12-E especially useful for paper production. However, the lack of surface penetration from the rollers would make the 12-E ineffective for restoration work, where users often need to get moisture readings deep in building materials to find hidden moisture pockets.
How to Avoid This Problem:
When choosing moisture meter electrodes, it’s important to consider each electrode’s design and the manufacturer’s recommendations. If the product description isn’t clear, consider contacting the manufacturer for details and use guidelines.
Most manufacturers will be happy to tell you what each of their electrodes is designed for and which of their moisture meters is compatible or best suited for the job.
Moisture Testing Mistake #4: Leaving Moisture Meter Pins Buried in Wet Materials
While moisture meters are designed for conducting moisture tests in damp materials, the pins of a pin-type meter should never be left sitting in water or wet building materials for prolonged periods of time. Limited exposure is a necessity, but long-term immersion can lead to corrosion of the pins. This, in turn, can compromise the pins’ ability to conduct electricity (resulting in inaccurate moisture content measurements).
Likewise, pinless moisture meters should not have their contact plates immersed in standing water. Leaving moisture on the scanning plate for too long could cause corrosion to form, impacting the pinless meter’s ability to make smooth contact with building materials and conduct accurate moisture tests.
How to Avoid This Problem:
The simplest way to avoid this issue is to not leave moisture meters in contact with the materials being tested. Also, when the meters are done being used, it’s a good idea to clean off the moisture testing medium (pins or scanning plate) with a dry cloth to remove any particulate matter and moisture that may be left after testing.
Finally, when the moisture meter isn’t being used, it should be stored in its case for safekeeping. This helps limit the meter’s exposure to the elements and prolong its useful life.
Moisture Testing Mistake #5: Failing to Take Material Temperature into Account
In most cases, the temperature of the materials being tested with a moisture meter doesn’t have a significant impact on moisture testing accuracy. However, in some cases, extremely high or low temperatures can throw off a moisture content measurement.
This is most common when ambient temperatures are outside of the 50° to 90° Fahrenheit (10° to 32.2° Celsius) range or when testing materials have recently been removed from such an environment.
How to Avoid This Problem:
The most common solution to this problem is to only take moisture measurements in room-temperature environments whenever possible. However, this is not always possible—lumber manufacturers may need to take readings of lumber fresh from the kiln or restoration experts may need to test for moisture in outdoor environments that are especially hot or cold.
In these cases, it may be necessary to use a thermometer to test the temperature of the environment or the material being tested and use that information to apply a temperature correction to the moisture measurement.
Moisture Testing Mistake #6: Not Checking the Moisture Meter’s Accuracy
Every moisture meter, no matter how well-maintained, will eventually lose accuracy. While performing basic maintenance and storing the meter in a carrying case can prolong its useful life, there will come a time where wear and tear from regular use will compromise the meter’s functionality.
However, many moisture meter users keep using their moisture testing tools for years without taking the time to check the moisture meter’s accuracy. This leads to them relying on erroneous moisture measurements that lead to bad decisions—such as deciding to bale hay that is too wet for safety so that hay combusts in the silo later.
How to Avoid This Problem:
The best solution is to regularly check the calibration of a moisture meter before it’s used for the first time each day. The methods for testing a moisture meter’s calibration vary, but the most common methods are:
- Using a Built-in Calibration Check: Some of the more advanced moisture meters on the market have built-in calibration checks. With this feature, users can simply push a button and the meter will perform a self-test that makes it easy to determine if it is giving accurate moisture measurements.
- Using a Secondary Calibration Testing Device: Some manufacturers make external testing devices for their moisture meters. For pin-type meters, a moisture content standard (MCS) is used to complete a circuit between the pins and should display a specific %MC when used. For pinless meters, moisture blocks are small blocks of wood that are designed to be paired with the meter and return a specific %MC value when scanned.
There is a third method that uses a second moisture meter to compare readings when testing the same materials. However, this method is less popular because it involves keeping a separate moisture meter just for making these comparison checks—and this extra meter must be the same make and model to provide the best comparison point. This is often seen as a waste of money when built-in calibration checks and moisture content standards are both less expensive and more reliable than keeping a second copy of a moisture testing tool.
Are you getting the most reliable and accurate moisture measurements from your moisture testing tools? Talk to the moisture meter experts from Delmhorst for information and advice that can help you get more accurate and reliable moisture measurements!
Subscribe to Our Blog
Post Related
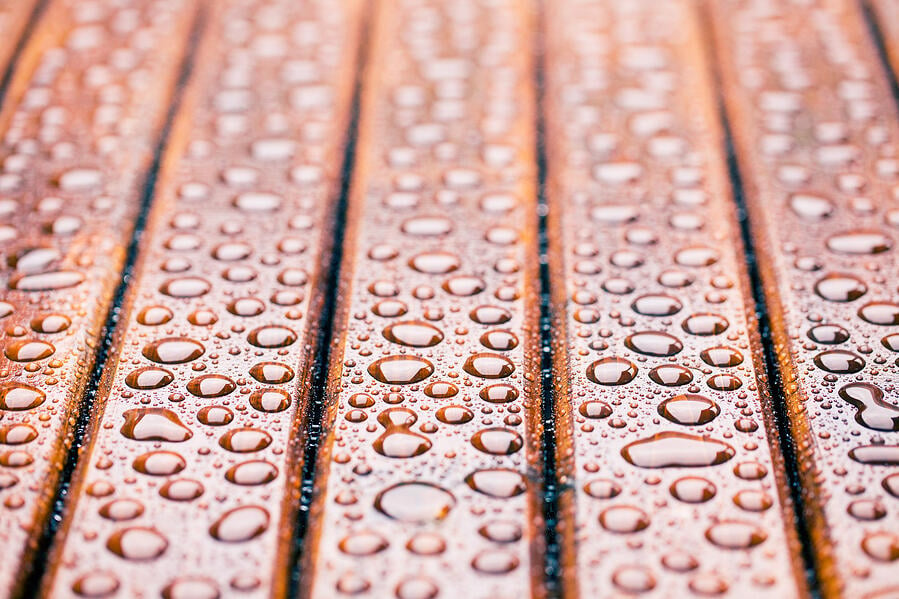
How to Check Lumber Acclimation with Moisture Meters
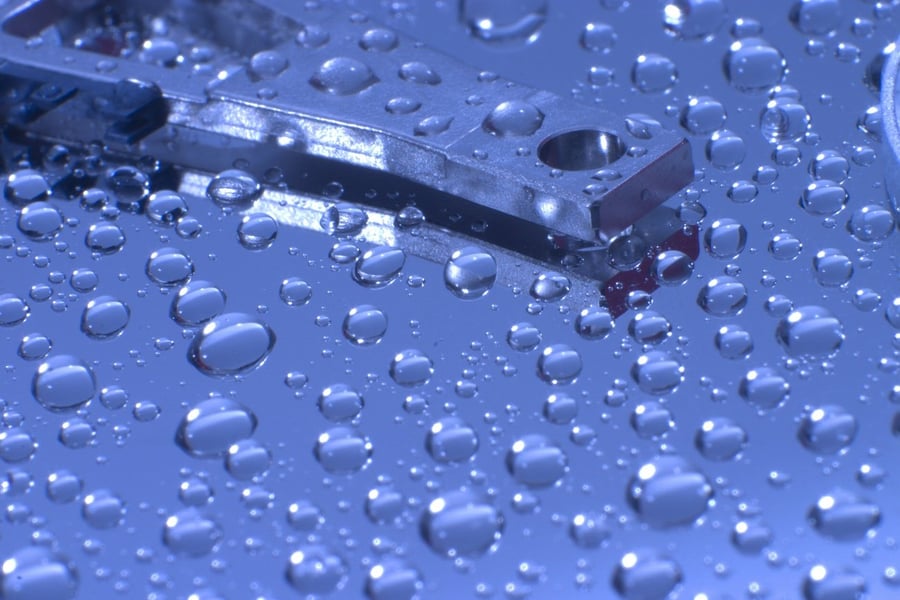